汽车零部件超声检测技术通过高频声波穿透金属材料,精准捕捉内部缺陷信号,已成为保障汽车安全性能的核心手段。该技术可检测直径0.1mm以上的裂纹、气孔、夹杂等缺陷,检测效率较传统方法提升3-5倍,广泛应用于发动机缸体、转向节、轮毂等关键部件的质量控制。
一、技术原理:声波与缺陷的“对话”机制
超声检测仪发射1-25MHz高频声波,当声波遇到缺陷界面时,部分能量反射形成回波信号。以某汽车厂转向节检测为例,采用5MHz纵波探头,可穿透40mm厚钢件,检测到深度15mm处的Φ0.3mm裂纹。系统通过分析回波时间差(Δt)与振幅(A),结合材料声速(C)计算缺陷位置(L=Δt×C/2)与尺寸,精度达±0.1mm。
二、核心应用场景:从铸造到焊接的全流程覆盖
1.铸件内部缺陷检测
在发动机缸体生产中,超声相控阵技术(PAUT)通过电子扫描生成内部缺陷三维图像。某合资车企应用该技术后,缸体缩孔漏检率从8%降至0.3%,单件检测时间缩短至90秒。
2.焊接接头质量评估
针对高强钢焊接件,采用TOFD(衍射时差法)检测根部未熔合缺陷。某新能源车企在电池包壳体焊接检测中,通过TOFD技术发现0.2mm层间未熔合,避免批量召回风险。
3.复合材料界面分析
碳纤维增强塑料(CFRP)轮毂检测中,低频超声(1MHz)可穿透复合材料层,结合C扫描成像技术,识别层间脱粘面积>1mm2的缺陷,检测灵敏度较目视检查提升200倍。
三、技术创新:从单探头到智能化的跨越
1.机器人自动化检测
某零部件供应商引入六轴机器人+相控阵探头系统,实现轮毂360°检测,定位精度±0.05mm,检测效率较人工提升8倍。
2.AI缺陷识别算法
基于深度学习的超声信号分析系统,可自动区分气孔、夹渣、裂纹三类缺陷,准确率达98.7%。某主机厂应用后,质检人员减少60%,误判率降低至0.5%以下。
3.多模态融合检测
将超声与涡流、红外技术结合,同步检测表面与内部缺陷。某安全件企业通过该方案,将转向节疲劳寿命预测准确率从72%提升至91%。
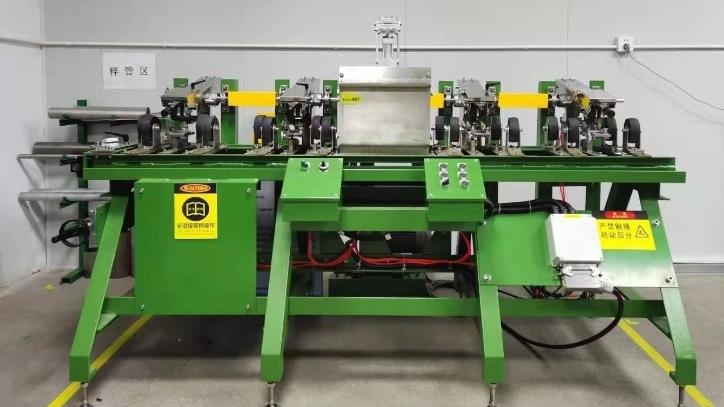
汽车零部件超声检测技术正朝着高精度、智能化、全场景方向发展。随着5G+工业互联网的普及,超声检测数据将实时上传云端,构建零部件全生命周期质量追溯体系。未来,量子超声、太赫兹成像等前沿技术有望突破现有检测极限,为自动驾驶、氢能汽车等新兴领域提供更可靠的安全保障,重新定义汽车工业的质量控制标准。